Safety Measures
Group-wide Production and Quality Risk Management
Risk Management Framework
Our Production and Quality Management Department is responsible for managing and reducing risks that threaten the stable production and quality of Group company products.
As a key activity, we hold monthly group production and quality meetings attended by quality assurance and safety control managers of operating companies with manufacturing departments.
At this meeting, the causes of accidents and complaints reported by each company are analyzed and information is shared.
We will also identify risk factors underlying accidents and complaints, and laterally deploy related information and countermeasures to prevent the recurrence of similar events.
This is a valuable opportunity for employees working in different industries to gain new insights by observing events from different angles.
In the event of a serious accident or complaint, such as the frequent occurrence of similar events within a short period of time, cases involving lost time injuries, or significant damage, we individually discuss the matter with each operating company to find a solution.
Responsible personnel of the Production and Quality Control Department will increase the frequency of visits to the production sites of each company, and work together with the personnel of the operating companies to detect and manage quality risks and confirm the effectiveness of measures to prevent recurrence.
Addressing risks
There are a variety of risks that can potentially interfere with day-to-day business activities, including the inability to procure raw materials due to discontinuation of production by suppliers, the inability to continue production due to the inability to find replacements for outdated equipment, or environmental pollution that halts production.
To address such risks, we are promoting risk impact assessment, in which each Group company predicts the frequency at which risks may materialize and the amount of damage they may incur if they do, then quantitatively evaluates the impact of risks on management, prioritize them to formulate and create countermeasures in advance.
This is done even at operating companies that do not have a manufacturing department, targeting risks that could hinder the provision of services to customers.
The results of risk impact assessments are reported at special meetings of the Group production and quality meeting held twice a year, attended by senior management, to enable speedy management decisions on budget measures and more.
Furthermore, in the event that a significant risk is detected that may affect the entire Group, it is also reported to the Group Risk Management Committee, which discusses overall risks related to business operations.
Maintaining a safe and hygienic work environment
Safety activities
The aforementioned Group production and quality meeting also addresses safety activities related to production activities.
Because our Group consists of companies in different industries, there are cases where countermeasures for accidents or complaints that occur at one company cannot be deployed directly to another.
However, by understanding production processes of different industries through discussions at Group production and quality meetings, new insights are discovered, leading to improvements across the entire group.
Safety activities include safety and health-related meetings and disaster drills conducted by each Group company in accordance with the Industrial Safety and Health Act.
Group companies in relatively similar industries share information by visiting respective factories and exchanging opinions on safety measures.
Working towards a safer workplace
Carlit Co., Ltd. creates a calendar of accidents and disasters that have occurred in the past so that they can be compiled into a record and not become a formality.
In addition, with the aim of increasing awareness of potential risks, we have introduced safety simulation devices that simulate the sensation of being in an accident.
Safety training programs to date have consisted mainly of lectures incorporating video materials for safety training and on-the-job training using standard manuals, which did not lead to a familiarity with accidents and disasters.
However, the introduction of safety simulation devices has enabled us to educate employees by actually experiencing the dangers that lurk in familiar everyday tasks.
This facility is also utilized by other Group companies and is operated to contribute to safety across the entire Group.
Other Group companies are also engaged in a variety of activities on a company-by-company basis, including the creation and use of hazard maps for plants, including partner companies, risk reduction efforts for all workers, and participation in safety training programs for major suppliers.
Although we are engaged in a wide range of safety activities, five accidents resulted in lost time in FY2023.
While preventing serious accidents is a priority, we will further promote improvement activities across the Group to eliminate all accidents and disasters.
We believe this will lead to improvements not only in production but also in the work environment.
Examples of safety simulation devices
- Entanglement safety simulation device
- Explosion safety simulation device
- Water pressure safety simulation device
- Pinching safety simulation device
- Slip and fall safety simulation device
*This table can be scrolled horizontally.
Item | FY2019 | FY2020 | FY2021 | FY2022 | FY2023 |
---|---|---|---|---|---|
Number of lost time accidents (Cases) | 3 | 2 | 1 | 2 | 5 |
Quality Assurance
Customer trust and satisfaction
We have established quality assurance as one of our basic CSR policies.
To earn the trust and ensure the satisfaction of our customers, we are actively working to improve the quality of our chemical products and other business fields.
Eliminate quality complaints
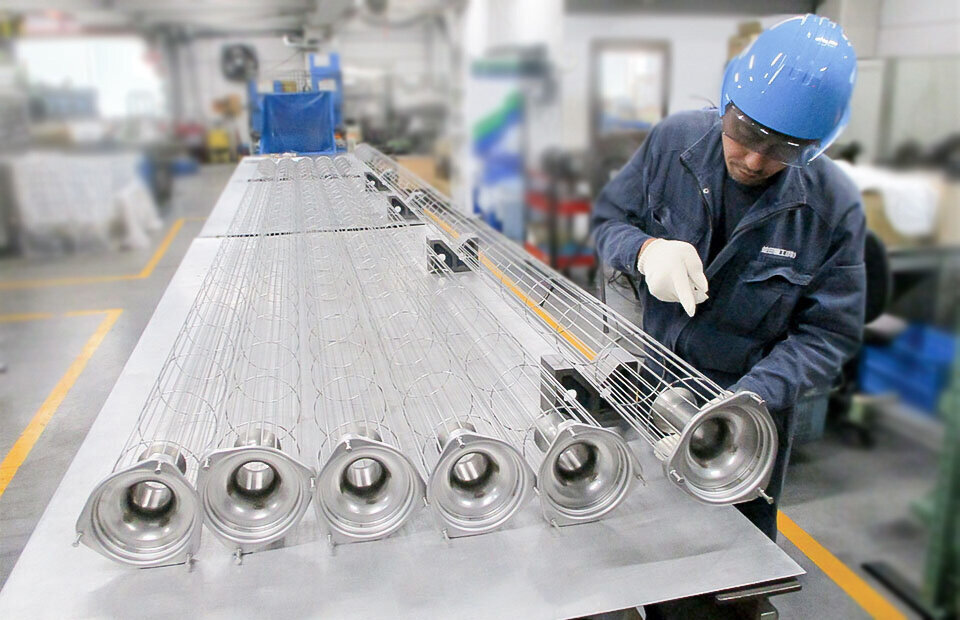
We consider "coexistence with society" an important social issue and pursue "contribution to safety and security" with the goal of eliminating quality complaints.Because we have products of which we are the only manufacturer and supplier as well as products that boast top market share in Japan, eliminating quality complaints is essential for earning customer trust.Japan Carlit Co., Ltd. (now Carlit Co., Ltd.), JC Bottling Co., Ltd., Carlit Sangyo Co., Ltd., Silicon Technology Corporation (now Carlit Co., Ltd.), Toyo Spring Industrial Co., Ltd., and General Design Co., Ltd. have obtained ISO 9001 certification, an international standard for quality management systems, and are working to continuously improve their quality assurance systems.The number of quality complaints increased in FY2023 over the previous year, so we will work to further strengthen Group-wide efforts to improve quality and eliminate complaints.
Group initiatives
At the Group Production and Quality Meeting, we conduct risk analysis for the Group as a whole, including investigating the causes of quality-related complaints at Group companies, which we use to carry out recurrence prevention activities. While each Group company has a different approach to quality management and level of quality activities due to the variety of business and company size, we aim to conduct meetings that facilitate improvement across the entire Group through the exchange of diverse opinions and regular discussions.
Acquired ISO9001 certification / Japan Carlit Co., Ltd.,(currently Carlit Co., Ltd.) Silicon Technology Corporation,(currently Carlit Co., Ltd.)
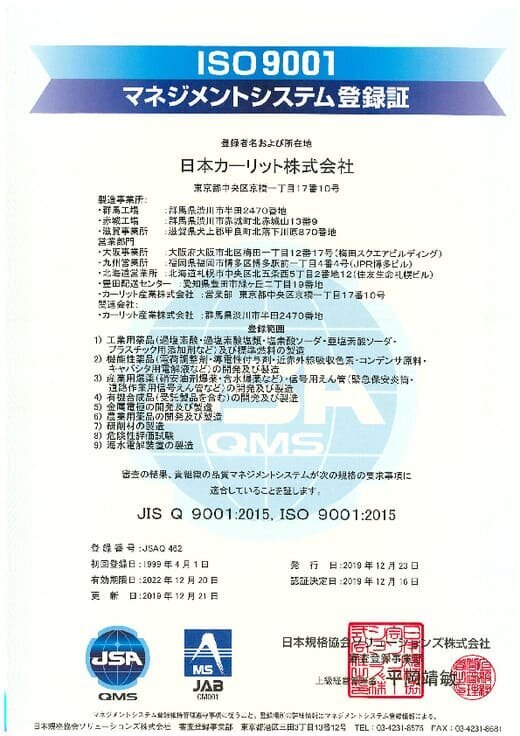
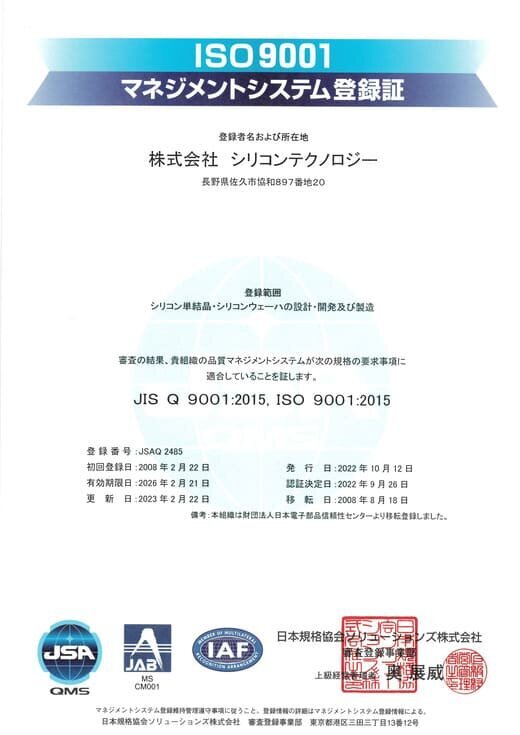
(right) Silicon Technology Corporation,(currently Carlit Co., Ltd.)
In addition, to strengthen our quality assurance system, Japan Carlit Co., Ltd., JC Bottling Co., Ltd., Carlit Sangyo Co., Ltd., Silicon Technology Corporation, Toyo Spring Industrial Co., Ltd., and General Design Co., Ltd. have acquired ISO9001 certification, an international standard for quality management systems, and have received favorable evaluations at annual audits.
Some companies were audited for customer quality audits and received favorable evaluations.
We will continue to further strengthen our initiatives to improve quality and eliminate complaints.
ISO registration certificate number details by location
Acquired FSSC 22000 certification / JC Bottling Co., Ltd.
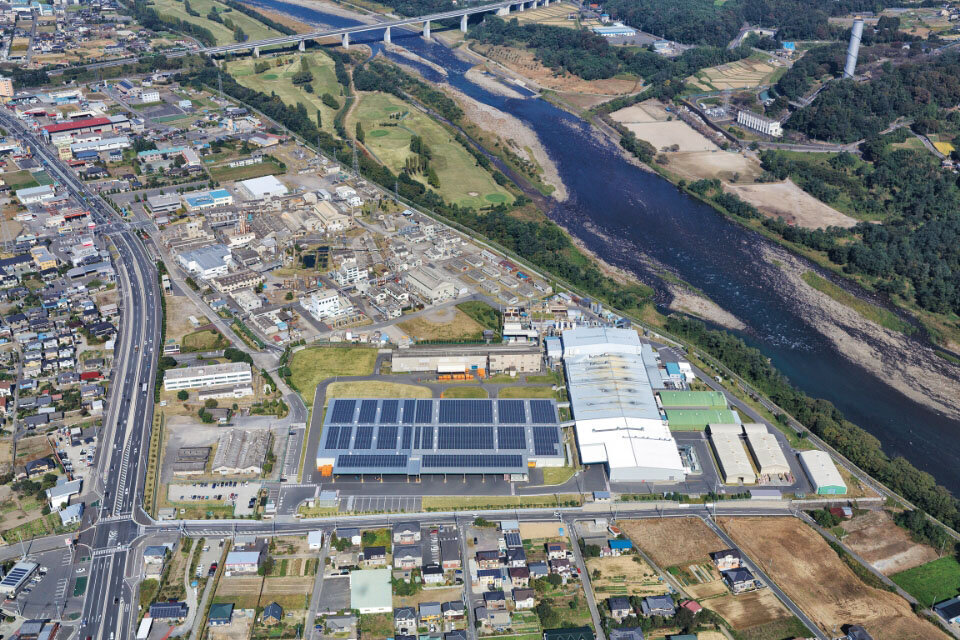
We acquired FSSC 22000 certification in December 2020. FSSC 22000 (Food Safety System Certification) is a certification for food safety management systems. This international standard was developed by the Netherlands' Foundation FSSC by combining the ISO 22000 (HACCP and PRPs) and ISO/TS 22002 series with the aim of establishing a certification scheme for food safety management systems in order to provide safe food to consumers.
In 2007, JC Bottling Co., Ltd. acquired the Comprehensive Sanitation Management and Production Process (CSMPP; Japan's version of HACCP) certification, a food safety management certification system promoted by the Ministry of Health, Labour and Welfare, and had been working on food safety measures in line with this. The CSMPP system was later abolished when adoption of the HACCP system became mandatory in June 2020 after the revised Food Sanitation Act was passed in June 2018. We thus obtained FSSC 22000 certification, an international standard, in place of CSMPP certification. We will continue to utilize this certification to ensure internationally accepted food safety, to certify the safety of our products, and as a strength of the company externally.